Successfully transforming your business into a lean thinking and acting company is not easy. I recently had the opportunity to meet with the senior management of 15 printing and graphics companies who had been implementing lean and continuous improvement manufacturing practices. While some had achieved higher rates of improvement, many others experienced limited success, and my discussions with the latter uncovered several common issues.
Many of the stalled companies had focused their lean implementation almost exclusively on applying lean tools and techniques during kaizen events. Methods such as 5S, make-ready reduction, kanban scheduling and standardized work were, and still are, used to improve targeted processes. While they can produce significant improvement in their early application, in most cases, these methods were simply grafted on to the existing systems of production and management. In short, the culture didn’t change.
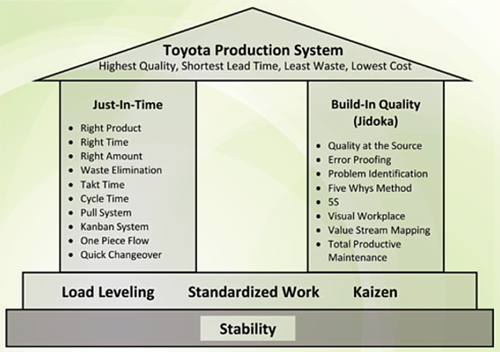
With only a superficial understanding of how lean manufacturing differs from traditional production practices, it’s not surprising this approach yields diminishing returns. Areas improved through 5S are unable to hold, let alone improve on, their gains, and eventually revert to their old state.
The Toyota Way
In 2001, Toyota published information about “The Toyota Way,” its approach consisting of two fundamental, completely intertwined elements: continuous improvement and respect for people.
Of the companies I spoke with, those disappointed with their results had implemented a lean/continuous improvement initiative without the respect for people element driving their efforts, while those with sustained improvement had made serious investments in developing people and tapping into their brainpower for problem-solving activities. This included a behavioral change as supervisors and managers shifted from a fire-fighting/directing role to a listening/coaching role — a difficult transition to achieve.
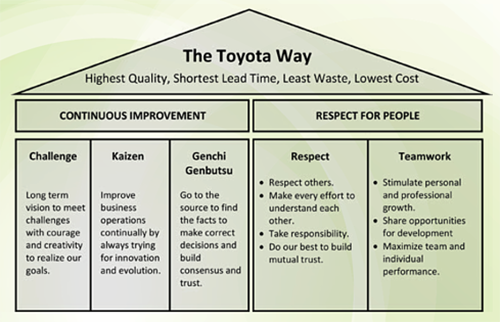
Let’s take a look at the Toyota Way’s five elements, i.e., the basis of lean manufacturing:
Challenge
Challenge is about highlighting specific improvement targets for every job based on the needs of the company for meeting customers’ requirements. Challenging brings an influx of energy and constructive tension to get teams focused on the right problems they need to solve. It leads to progress and satisfaction with the work being performed, which leads to personal growth.
Kaizen
For the challenge to be appropriate for a person or team, it should be beyond their current capabilities, and therefore require kaizen. Kaizen literally means “change for the better,” but implies something more: a systematic methodology for learning how to achieve a new level of performance. Thus, kaizen refers to the process of improving.
Genchi Genbutsu
This Japanese phrase simply means go and see for yourself — going to the source to fact check and be sure you have all the right information to make a good decision. It means that people, especially managers, shouldn’t spend all their time in offices and conference rooms. They should frequent the places of real work (i.e., the production floor), stay there and see and understand what is really going on and needs improvement.
Respect
Respect for people means respect for the brainpower and capability of all employees. It’s the fundamental belief that people have the capacity to think, develop and improve — the basic enabler of continuous improvement. It’s not about being nice, nor about having great “people skills.” It’s challenging people to perform to their peak ability.
Teamwork
Teamwork means respecting others’ opinions and embracing shared objectives. It's knowing how to solve problems with colleagues across departmental borders, creating stronger working relationships across the business. By coaching team members to identify and solve problems, lean managers challenge them to think and act differently when they encounter issues at work. Thus, individual employees and teams continually improve their problem-solving and critical-thinking skills through guided practice.
Learn more about lean thinking and continuous improvement at the 2019 Continuous Improvement Conference (April 14 - 17, Dallas).