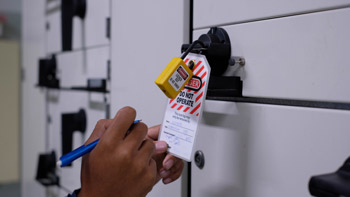
Where do you land? Are these in your top 10? If any of these standards are new to you, or if you just need a refresher, sign up today for PRINTING United Alliance’s 2021 Safety Recognition Program (registration ends Jan. 31).
1. Lockout/tag-out (29 CFR 1910.147). Failing to lockout equipment, have a written program, and conduct annual inspections of machine-specific procedures is the most common violation.
2. Hazard communication (29 CFR 1910.1200). Common citations include not having a written program, safety data sheets for all chemicals, employee training, and secondary container labels.
3. Machine guarding (29 CFR 1910.212). Do you have physical guards at all hazard points, such as ingoing nip points, to protect employees from exposure to, and contact with, the hazards associated with moving parts? Are the guards that came with the equipment installed on it?
4. Personal protective equipment (29 CFR 1910.132). Failure to conduct the assessment and certify it is a commonly overlooked requirement.
5. Powered industrial trucks (29 CFR 1910.178). Safety violations include improper vehicle use, lack of training, and failing to recertify operators every three years.
6. Electrical safety (29 CFR 1910.305). Common violations under this standard involve blocked access to breaker boxes, open breakers, missing knockouts in junction or breaker boxes, and no or incomplete labeling of breakers.
7. Electrical safety (29 CFR 1910.303). Common violations under this standard involve the use of extension cords, power strips, improper pendant drops, and frayed wiring.
8. Fire Prevention Plan (29 CFR 1910.39). Not having a written fire prevention plan listing of all major fire hazards, proper handling and storage procedures for hazardous materials, potential ignition sources and their control, the type of fire protection equipment necessary to control each major hazard, and employee training made it into the top 10. Companies with 10 or fewer employees can communicate the requirements verbally.
9. Portable fire extinguishers (29 CFR 1910.157). Common violations include blocking access to fire extinguishers, not having them checked annually, and not providing annual training for employees expected to use them.
10. Machine guarding (29 CFR 1910.219). One of OSHA’s other machine guarding standards is preventing exposure to hazards from power transmission components found on equipment that include pulleys, flywheels, and drive shafts. Failure to provide a physical guard to prevent employee contact with these moving machine parts is a common violation.
10. Respiratory protection (29 CFR 1910.134) If respirators, other than dust masks, are to be provided to employees, there are very specific steps that must be followed. Failing to establish a written respiratory program was one of last year’s most common violations, followed by the failure to provide proper medical evaluations to those using respirators.
Take a few moments to review this list and compare it to your safety program. Is your program doing great, or does it need fine tuning? Focusing your safety program to address these common deficiencies will help prevent injuries, citations, and penalties.
Be sure to sign up for the 2021 Safety Recognition Program by contacting the PRINTING United Alliance Government Affairs Department (govtaffairs@printing.org) before the end of the month — you will be glad that you did! Not only will you earn recognition for your safety efforts, but you will learn about the many resources, including written program templates, designed to assist you with your safety and health activities.
The Government Affairs Department continues to report on OSHA's COVID-19 requirements and will monitor/report on OSHA activity under the incoming Biden-Harris administration.
Gary A. Jones is the director of environmental, health, and safety affairs for PRINTING United Alliance. His primary responsibility is to monitor and analyze EHS regulatory activities at all domestic and some international government levels. He provides representation on behalf of the printing and specialty graphic imaging industry.
In doing so, Jones works closely with the federal and state-level Environmental Protection Agencies, Occupational Safety and Health Agency, Department of Transportation, and other agencies. He also provides membership assistance on EHS compliance and sustainability programs.